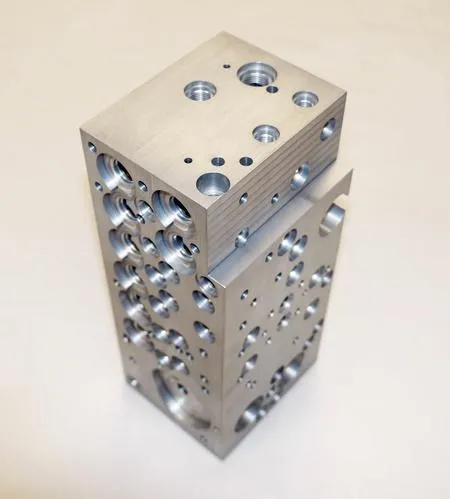
Dive into the history and technological advancements in manifold design.
The Evolution of Manifold Design: From Basics to Breakthroughs with Summit Machine Works
Manifolds are the unsung heroes of many fluid and gas systems, providing a centralized, efficient way to control direction, pressure, and flow. But these critical components haven't always been the sophisticated devices we see today. Let's dive into the history and technological advancements in manifold design and see how Summit Machine Works brings cutting-edge solutions to this field.
A Glimpse into the Past: Early Manifold Concepts
Early fluid power and gas distribution systems often relied on extensive networks of individual pipes, fittings, and valves. While functional, this approach presented significant challenges:
Complexity: Systems were sprawling and difficult to assemble or troubleshoot.
Leak Points: Every connection point (fitting, valve port) was a potential source of leaks, leading to inefficiency and safety concerns.
Space: These piped systems required considerable space.
The concept of a manifold emerged as a solution – consolidating multiple flow paths and valve connections into a single block of material. Early manifolds were relatively simple, often just blocks of metal with manually drilled intersecting passages.
Revolutionizing Flow: Key Technological Advancements
The journey from basic blocks to modern, high-performance manifolds involved several key technological leaps:
Integrated Hydraulic Circuits (IHC)
Perhaps the most significant shift was the development of integrated circuits. Instead of just connecting external valves, designers began incorporating valve cavities directly into the manifold block. This dramatically reduced the number of external connections, minimizing leak points, saving space, and simplifying system assembly. Specialized cartridge valves were developed to fit neatly within these cavities.
Precision Machining and CNC Technology
The advent of Computer Numerical Control (CNC) machining revolutionized manifold manufacturing. CNC machines allowed for:
Complex Geometries: Drilling intricate, multi-axis internal passages with high accuracy became feasible.
Repeatability: Ensuring consistent quality across multiple units.
Efficiency: Faster production times compared to manual methods.
This precision enabled more compact and efficient designs that were previously impossible.
Materials Science
While cast iron and steel were common early materials, advancements brought forth new options like aluminum alloys (lighter weight), stainless steel (corrosion resistance), and even specialized plastics or composites for specific applications, improving performance and durability.
Computer-Aided Design (CAD) and Fluid Dynamics (CFD)
Modern design relies heavily on CAD software to model complex manifolds in 3D. Furthermore, Computational Fluid Dynamics (CFD) simulation allows engineers to analyze flow paths, predict pressure drops, and optimize performance before any metal is cut, reducing prototyping time and cost.
Modern Manifolds: Customization and Performance
Today, manifolds are highly engineered components tailored to specific applications. They can range from simple directional control blocks to incredibly complex units integrating dozens of valves, sensors, and sophisticated flow logic. Customization is key, ensuring the manifold perfectly meets the system's requirements for flow rate, pressure, size, weight, and environmental conditions.
Summit Machine Works: Your Partner for Advanced Manifold Solutions
Understanding the history and technology behind manifold design is crucial for creating effective solutions. At Summit Machine Works, we leverage these advancements to provide comprehensive manifold services:
Custom Design: Our engineering team utilizes modern CAD and potentially CFD tools to design manifolds tailored precisely to your application's needs.
Precision Manufacturing: Utilizing state-of-the-art CNC machining centers, we manufacture manifolds from a variety of materials to exacting tolerances, ensuring optimal performance and reliability.
Prototyping and Production: Whether you need a single prototype or full production runs, Summit Machine Works has the capacity and expertise.
Quality Assurance: Rigorous testing and inspection ensure every manifold meets the highest standards.
From hydraulic power units to pneumatic control systems and specialized gas distribution networks, Summit Machine Works has the expertise to deliver the high-quality, custom manifold solutions you require.
Conclusion: The Future of Efficient Control
Manifold design has evolved significantly, driven by innovation in materials, machining, and design tools. These advancements continue to enable more compact, efficient, and reliable fluid and gas control systems across countless industries.
If you need expert design and manufacturing for your next custom manifold project, contact Summit Machine Works today. Let us put our expertise to work for you!