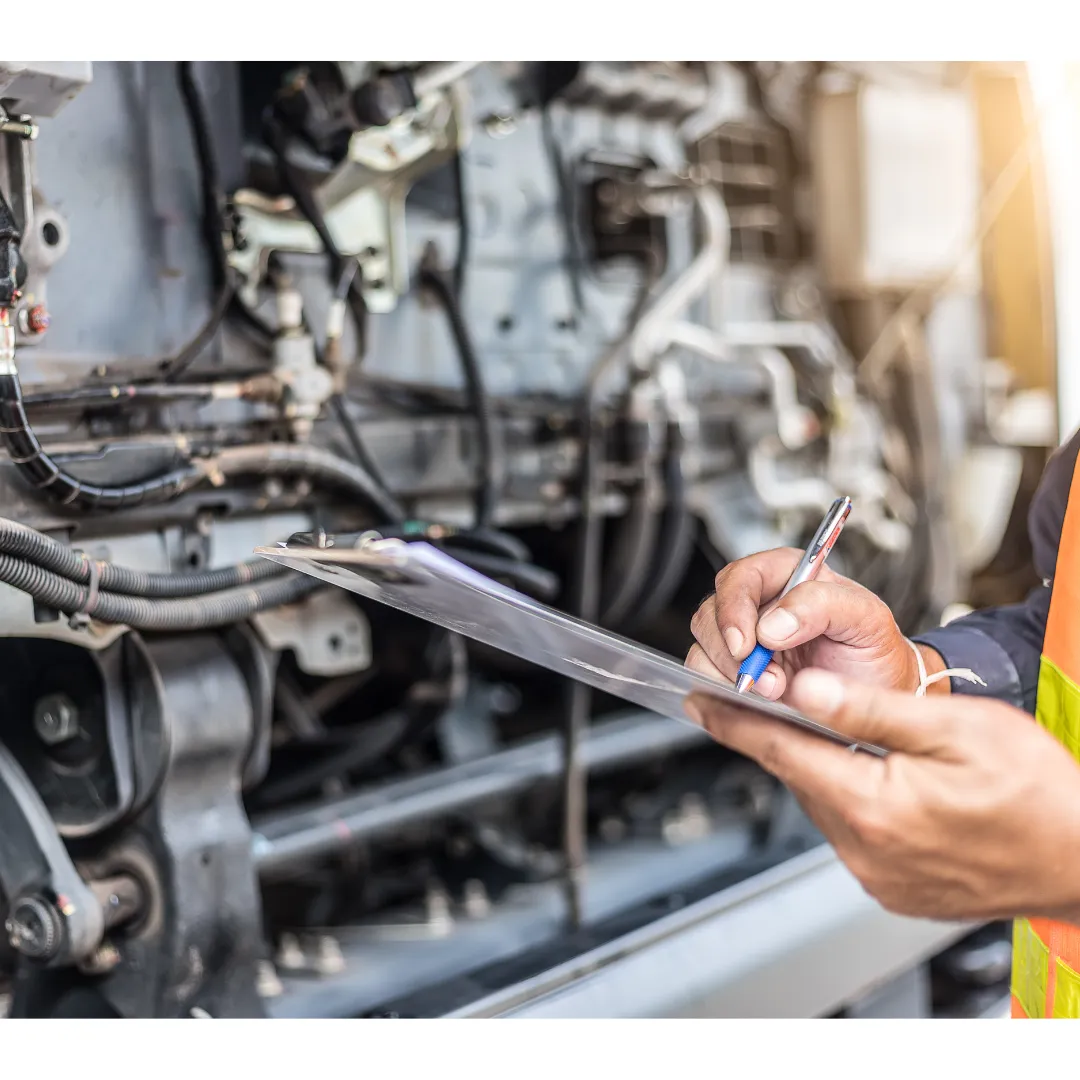
Preventative Maintenance Tips for Hydraulic Equipment
Hydraulic systems are essential to the functioning of many industrial machines. From construction equipment to manufacturing machinery, hydraulics provide the power required for heavy lifting, precision movements, and repetitive tasks. Without proper maintenance, these systems can experience breakdowns that not only reduce efficiency but can also lead to costly repairs and downtime. This post explores key preventative maintenance tips to ensure the longevity and reliability of your hydraulic equipment.
1. Regular Fluid Checks and Replacements
The hydraulic fluid is the core component that allows the entire system to operate smoothly. Over time, hydraulic fluid can degrade or become contaminated with particulates like dirt, metal shavings, or water. This contamination can result in poor system performance and eventual damage to critical components such as pumps and cylinders. Implement a schedule to regularly check fluid levels and fluid quality. Consider changing hydraulic fluids as recommended by the manufacturer or sooner if performance issues are noted. The cost of regular fluid maintenance is minor compared to the potential cost of a system failure.
2. Monitor and Replace Filters
Hydraulic systems are extremely sensitive to contamination, which can enter through degraded fluid or poor filtration. Dirty hydraulic fluid is one of the leading causes of component wear and failure. Filters are responsible for catching debris before it circulates through the system and damages pumps, motors, or cylinders. Checking and replacing filters on a regular schedule ensures the system stays clean. If the filter becomes clogged, it can cause increased pressure in the system, leading to premature wear or failure of other components.
3. Inspect Hoses and Fittings for Wear and Leaks
Hoses and fittings are crucial in delivering hydraulic fluid throughout the system under high pressure. Any cracks, abrasions, or leaks in these parts can lead to significant fluid loss and reduced system efficiency. Regularly inspecting hoses and fittings for visible wear, leaks, or weak spots can prevent sudden failures that could halt operations. It's important to replace any components showing wear to avoid unexpected breakdowns.
4. Maintain Proper Temperature Control
Hydraulic systems can generate a significant amount of heat during operation. Excessive heat can cause the hydraulic fluid to break down, reducing its ability to lubricate and protect internal components. Overheating can also damage seals, hoses, and other sensitive parts. Regularly monitor the system’s operating temperature and ensure that cooling mechanisms, such as fans or heat exchangers, are functioning properly. Keeping the system within its recommended temperature range will help maintain optimal performance and reduce wear.
5. Perform Regular System Inspections
Preventative maintenance should include regular, thorough inspections of the entire hydraulic system. Operators should listen for unusual noises, feel for vibrations, and observe for signs of wear, such as fluid leaks or excessive heat. Keeping detailed maintenance logs will help track the health of the system and identify patterns that could indicate the need for repair or replacement. Inspections also allow operators to catch minor issues before they become major problems.
6. Utilize Preventative Maintenance Software
Today’s technology offers maintenance management software that can help track inspection schedules, maintenance logs, and parts replacements. By using preventative maintenance software, you can ensure that the entire hydraulic system is properly cared for without missing any scheduled checks. This kind of software is particularly useful for businesses with multiple hydraulic systems, as it allows operators to automate reminders for maintenance tasks and create a historical record of system performance.
Conclusion
Preventative maintenance is essential for the longevity and reliability of hydraulic equipment. Following best practices—such as regular fluid checks, filter replacements, hose inspections, temperature control, and systematic inspections—can drastically reduce the risk of unexpected failures. By keeping your hydraulic system in optimal condition, you can reduce downtime, increase operational efficiency, and save on costly repairs. Investing time in regular maintenance today will pay off in the long term, ensuring your equipment serves your needs for years to come.