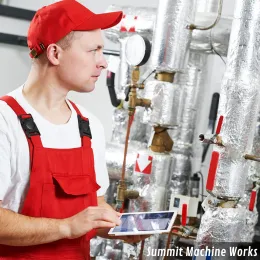
The Importance of Regular System Inspections for Hydraulic Systems
The Importance of Regular System Inspections for Hydraulic Systems
In hydraulic systems, reliability is crucial. From industrial manufacturing to heavy-duty construction, these systems play a vital role in ensuring smooth, efficient operations. To maintain peak performance and avoid costly downtime, regular system inspections are essential. Routine inspections not only extend the life of equipment but also provide an opportunity to catch minor issues before they develop into major problems.
Why Regular Inspections Matter
Hydraulic systems operate under high pressure and are subject to intense demands. Over time, even minor wear can lead to significant failures if left unaddressed. Regular inspections allow operators to identify early warning signs, make necessary repairs, and ensure that the system is performing optimally. By scheduling these checks consistently, companies can prevent unexpected breakdowns and improve the overall efficiency and safety of their operations.
Key Areas to Inspect in a Hydraulic System
To perform an effective inspection, it’s important to focus on these critical areas:
1. Listen for Unusual Noises
Hydraulic systems should operate smoothly and quietly. Unusual sounds, such as knocking, hissing, or squealing, can indicate issues like air in the lines, worn-out components, or blockages. Listening for these sounds during operation can alert operators to issues that may require immediate attention.
2. Feel for Vibrations
Excessive vibrations are another common indicator of hydraulic system problems. Vibrations can stem from misaligned components, worn bearings, or loose fittings. By physically feeling for vibrations in key areas of the system, operators can quickly detect when adjustments or repairs are necessary to prevent further wear or damage.
3. Watch for Fluid Leaks
Fluid leaks are one of the most visible signs of wear in a hydraulic system. Leaks can occur in hoses, fittings, or seals, and they indicate a loss of hydraulic fluid that can compromise system pressure and performance. Addressing leaks promptly is essential to keep the system running smoothly and prevent costly fluid replacement.
4. Monitor for Excessive Heat
Hydraulic systems generate heat during operation, but excessive temperatures can signal trouble. Overheating can cause fluid breakdown, damage seals, and reduce the efficiency of the system. Operators should monitor the system temperature and ensure that cooling mechanisms, such as fans or heat exchangers, are functioning properly.
The Value of Maintenance Logs
Keeping a detailed maintenance log is a key part of an effective inspection program. By documenting each inspection, operators can track patterns and identify recurring issues. Maintenance logs provide a historical record of the system’s health, helping to forecast when parts may need replacement or when more in-depth repairs may be necessary. This proactive approach to maintenance helps reduce unplanned downtime and contributes to a more efficient workflow.
Benefits of Regular Inspections
Implementing a routine inspection program offers several benefits:
Reduced Downtime: Catching issues early helps prevent unexpected breakdowns that can halt operations.
Extended Equipment Life: Regular maintenance reduces wear and tear, extending the lifespan of hydraulic components.
Increased Safety: By identifying potential issues, inspections help ensure safe operation for all personnel.
Cost Savings: Preventative maintenance is often much less expensive than emergency repairs or system replacements.
Conclusion
Regular system inspections are an investment in the longevity and reliability of hydraulic equipment. By listening, feeling for vibrations, watching for leaks, and monitoring heat, operators can identify issues before they escalate, ensuring optimal performance and safety. Keeping detailed maintenance records will further enhance the effectiveness of the inspection program. For companies relying on hydraulic systems, regular inspections are a crucial step toward achieving maximum productivity and minimizing downtime.
At Summit Machine Group, we believe in the power of proactive maintenance to support our clients' success. By following these inspection practices, companies can get the most out of their hydraulic systems and maintain smooth, efficient operations year-round.